In-field Service Torque Guide

The purpose of this document is to define generic and product‐specific torque settings for in‐field replacement and repairs. This is NOT a guide for in‐field fastener torque verification as many threaded fasteners installed by Meyer Sound have thread‐locker applied to them; verifying torque values in the field may jeopardize the thread‐locker's effectiveness and the product’s safety.
Unless described specifically below in section 4.0, torque all fasteners per the range described in section 3.0.
Tools required

Calibrated torque screwdriver for low torque settings below 40 in‐lbs [4.5 N‐m]
Calibrate torque wrench for torque settings above 40 in‐lbs [4.5 N‐m]
Necessary bits for fasteners being tightened (e.g., hex drive, Philips bit, socket drive)
Thread locker, if included in the replacement kit. See section 5.0
Generic torque settings

Unless specified below in section 4.0, torque all fasteners per the tables below.
Table 1 applies to machine screws and bolts (Unified English, Metric threads). These will be the most common types of fasteners used on Meyer Sound products.
Table 2 applies to thread forming screws, such as wood and plastic thread forming screws. Generally, lower torque values are used for these fasteners to prevent stripping. These are not commonly found on Meyer Sound products.
Note
Torque specifications in loudspeakers can change over time due to time‐induced relaxation in materials like gaskets, plastics, and wood or from heavy vibrations associated with fasteners on loudspeaker products.
SCREW SIZE | COMMON SUB‐ASSEMBLIES | TORQUE RANGE (IN‐LBS [N‐M]) |
---|---|---|
#4, M2.5, M3 | Chassis Products, Electronics | 4‐6 [.5‐.7] |
#6 | High Driver Assemblies, Grilles, Electronics | 10‐12 [1.1‐1.4] |
#8, M4 | 14‐18 [1.6‐2.0] | |
#10, #12, M5 | Rigging Components, Low Drivers | 20‐24 [2.3‐2.7] |
¼‐20; ¼‐28, M6 | 25‐30 [2.8‐3.4] | |
5/16‐18, M8 | Rigging Components | 120 [13.6] |
3/8‐16, M10 | 180 [20.3] |
SCREW SIZE | COMMON SUB‐ASSEMBLIES | TORQUE RANGE (IN‐LBS [N‐M]) |
---|---|---|
#4, M2.5, M3 | Electronics | 4‐6 [.5‐.7] |
#6, #8, M4 | High Driver Assemblies, Electronics | 8‐12 [.9‐1.4] |
#10, #12, M5 | Rigging Components, Low Drivers | 14‐18 [1.6‐2.0] |
Sub-assembly specific torque settings

Table 3 lists certain structural items with specific torque requirements. These mainly pertain to structural safety items, such as end frames, grids, and transition frames. If you are unsure what item is described below or you cannot find your item, contact Meyer Sound.
Item Description | Part number(s) | Product used on | Torque range in LBS [N‐M] |
---|---|---|---|
3/8‐16 SOCKET HEAD RIGGING KNOB | 61.152.022.01 | ‐ M’ELODIE ENDFRAME | 180‐200 [20.3‐22.6 ] |
3/8‐16 HEX HEAD RIGGING KNOB | 61.243.098.01 | ‐ LEOPARD ENDFRAME ‐ 900‐LFC ENDFRAME | 125‐150 [14.1‐16.9 ] |
1/2‐13 HEX HEAD RIGGING KNOB | 61.232.041.01 | ‐ LYON ENDFRAME | 330‐360 [37.3‐40.7 ] |
5/8‐11 HEX HEAD RIGGING KNOB | 61.215.028.01 | ‐ 1100‐LFC ENDFRAME ‐ LEO‐M ENDFRAME | 570‐600 [64.4‐67.8 ] |
1/4‐20 BUTTON HEAD SOCKET CAP SCREW | 101.244 101.744 | ‐ ENDFRAME TO ENCLOSURE | 28‐36 [3.2‐4.1] |
3/8‐16 BUTTON HEAD SOCKET CAP SCREW | 101.219 101.719 | ‐ ENDFRAME TO ENCLOSURE | 170‐190 [19.2‐21.5 ] |
3/8‐16 X 1.25” BUTTON | 101.195 | ‐ 900‐LFC ENDFRAME TO | 60‐80 [6.8‐9.0 ] |
HEAD SOCKET CAP | 101.695 | ENCLOSURE | |
SCREW |
Thread-locker application

Most fasteners installed on Meyer Sound products use a locking mechanism such as lock washers, locknuts, thread locker, etc., to minimize the vibration loosening seen on loudspeaker products. In several cases, Meyer Sound uses medium and high strength thread locker and will supply capsules with replacement kits or parts when applicable.
When applying thread-locker, the following guidelines are recommended:
Clean any old thread-locker from the existing threads with a wire brush.
Apply a 360o bead of thread locker to the second leading male thread, as shown in Figure 1.
Note
The minimum ambient temperature for the application of the thread locker is 50o F [10o C]
Clean any old thread-locker from the existing threads with a wire brush.
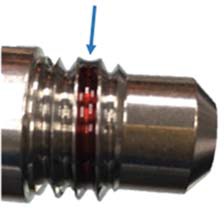
Thread-locker application on the second leading thread
Note
Some fasteners will have a locking patch pre‐applied to their threads. These screws may be un-installed / re‐installed about 5 times before the locking patch becomes less effective. Meyer Sound recommends obtaining new fasteners for fasteners being serviced that have pre-applied patches and requires replacing any patched rigging fasteners.